San Francisco, California. – San Francisco’s St. Luke’s Hospital complex is made up of four buildings, ranging from 90 to 25 years old. Heating the building required 26,000,000 Btuh, a costly need that had been met for half a century by a high-pressure steam boiler.
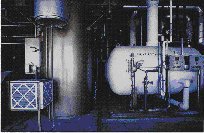
Regulations in the State of California require a stationary licensed boiler attendant 24 hr a day, 365 days a year on any direct-fired steam system that generates more than 15 lb of high-pressure steam. As of last year, the cost of St. Luke’s boiler attendants in wages and benefits had risen to $350,000 annually. The State of California does not require a licensed boiler operator with a thermal fluid heating system that operates within a closed loop at a very low pressure. Hot oil is pumped through unfired steam generators to create steam without high pressure.
The hospital saw the need to change from direct-fired steam generation to a modern thermal fluid heater. The job called for removing the 12 by 25 ft steam boiler and installing three 6,000,000 Btuh Fulton thermal fluid heaters, plus two 10,000,000 Btuh oil-to-unfired steam heat exchangers. The job took five months to complete; fortunately, the steam header and steam condensate piping did not have to be replaced. Because the steam is generated in unfired pressure vessels, the 60 lb of high-pressure steam can be provided by the new system without a stationary attendant as required by direct-fired steam boilers.
Honeywell provided micro-based DDC controls and Model 7,800 Burner Controls for the new system and served as the general contractor. The changeover to thermal fluid heaters also enabled the hospital to reassign the licensed boiler operators to other duties.
The direct-fired steam boiler was oversized and consumed energy insufficiently every time it recycled. With the new system, one 6,000,000 Btuh unit stays in constant operation; the others only come on line when the load makes it necessary. This has led to a projected annual saving of 18 percent of the hospital’s natural gas bill.
The new thermal fluid heaters are charged with Paratherm NF Heat Transfer fluid. Mike Andress, project manager for Honeywell, stated the fluid was doing an excellent job – no complaints. Since the NF fluid is rated for 600 F and delivers precise uniform temperature control, it has no trouble providing the 300 F heat required. In addition, the fluid has very high heat transfer coefficients for improved efficiency. It is also non-toxic, non-fouling, and non-hazardous. At the end of its use cycle, it can be mixed with other spent lube oils and sent to a local recycler – another cost saving tot he hospital.
At St. Joseph’s Medical Center in Stockton, Calif., the change from high-pressure steam boilers to Fulton thermal fluid heaters and Fulton 9 1/2 hp boilers was made in 1994. While the new system generated enough steam for most hospital functions, additional steam pressure was required to operate the laundry.
Jerry Cotton, manger of maintenance at St. Joseph’s, stated that the changeover involved installing three Fulton 9 1/2 hp tubeless steam boilers. These units generate less than 15 hp and therefore do not necessitate the 24 hr boiler attendant required by California law. Once the system was up and running, St. Joseph’s laundry discovered one minor problem – the new system could not generate the 125 psi steam pressure required by the ironer; it was limited to a maximum of approximately 80 psi. The problem was corrected with the installation of a supplemental thermal fluid heater. This hot oil heater operates in a closed loop system and supplies heat to the ironer, which is within a 2 F temperature range. The unit has been in service for over two years without problems. Like St. Luke’s, St. Joseph’s charges all the thermal fluid heaters with Paratherm NF heat transfer fluid.
A different situation exists at the Sutter Roseville Hospital in Roseville, Calif. This new facility is a 340,000 sq ft general hospital with four new thermal fluid heaters. Dale Holt, the maintenance and operations supervisor, stated that the system was designed to operate two heat transfer units and use the other two as backups. The backups are set to take over automatically if the steam temperature generated by the primary units falls below a certain point.
To generate 280 F steam, the hospital maintains the heat transfer fluid at 450 F. The closed loop thermal fluid system is used to provide all of the 700 bhp of central plant steam required for building heat, kitchen, and sterilization. To protect the hospital from environmental problems, the hot oil heaters were designed with low emission burners to meet 30 ppm NOx requirements.
The hot oil heaters, expansion/deaerator tank, hot oil pumps, and unfired steam generators were skid mounted and pre-piped at the Fulton factory. Piping was disassembled for shipping but match marked for easy reassembly at the job site. The system is fired with natural gas, and there is a 20,000 gal oil storage tank that can take over in case of emergency.
The system has been up and running since June 21 of this year. Holt stated that in general the system is running well, and the heat transfer fluid in the system is performing up to expectations.
The Sutter Rosevill Hospital, like St. Joseph’s Hospital and St. Luke’s Hospital, found that a thermal fluid heating system costs significantly less to operate than a direct-fired steam boiler system.